How Architrave is made
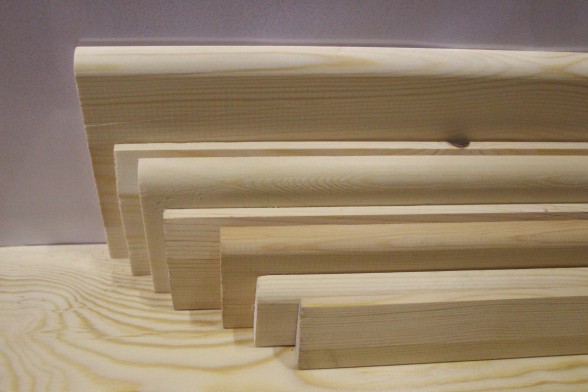
Architrave - before it gets to you.....
George Hill Timber supplies materials to hundreds of customers every week. You may have been one of them or hopefully will soon be one of them. We thought it would be interesting to give our customers an insight into just what goes on behind the scenes to provide you with the timbers you require. As an example we are going to follow the path of a length of Architrave from the forest to it becoming the final crowning glory of a door surround.
It is wintertime in Sweden, the next batch of trees have just been selected for felling in the sustainable forest. Most felling is carried out during the winter months as this is when trees have their lowest moisture content, that is, that they retain less water in their cells in winter than during the summer. Trees are first carefully selected for good health, straightness and height. Once felled the trees are left to "air dry" for a few months while the moisture inside them evaporates away at a natural speed.
From here the timbers go through a sawmill, where they are put through machinery which strips them of their bark. All the bark is recycled, bagged and distributed worldwide to garden centres to be used as mulch. During the next stage the bare logs are selected into different grades, which will determine what the final timbers will be used for. As an example the logs that contain the fewest knots will be used for skirting boards and architraves. The logs then go through a cutting process, where they are sawn down their length. This produces various sized timber planks from one log. Sizes from 75 x 225 right down to 25 x 75 can be produced from a single tree. The planks are cut in specific ways across their diameter to elevate cupping of the final timbers. All the various sizes are sorted and put into individual packs, for example all the 75 x 225 planks will be bundled into one pack.
From here they will go through a "kiln drying" process. Kiln drying involves placing large packs of timber into heated kiln, which reduces the moisture content of the timbers even more. This helps to stabilise the timbers and helps to make them stronger.
The packs are then weighed, wrapped, labelled and transported to the docks to be shipped overseas to merchants like ourselves at George Hill to become Architrave.
From the initial felling process, to the timber arriving into our yard, can be anything from 18 months onwards. We have just received a pack of 25 x 75 Redwood, which is currently being machined in our own sawmill, it is now in the process of being fed through a machine called a "moulder". Sawn timber is fed through the machine, and passes through various "cutting heads", these are circular drums of metal which house specially designed pieces of steel which cut the profile of the moulding into the timber. The sawn plank emerges at the other end of the machine as a pristine, planed and moulded piece of architrave !!.
So hopefully next time you visit us to purchase your timber, you will have more of an understanding as to what has gone on behind the scenes to provide you with our high quality Architrave and other materials.
Enquire now for our range of architrave or please feel free to phone, call in and visit us.